出荷作業効率化できる倉庫レイアウト改善の基本とコツ
倉庫レイアウトの見直しや改善は、在庫を正しく管理し、ピッキングなどの作業効率を高く維持するためにも大変重要です。逆に作業効率が落ちたり、保管スペースが足りなくなったりした時は、レイアウトを改善するタイミングかもしれません。また、日々新しく変わる現場に合わせて、定期的に見直す必要もあります。
今回は、作業を効率化するための倉庫レイアウトの基本とコツを詳しくご紹介します。
倉庫レイアウトを改善するメリット
倉庫レイアウトを改善するのは大掛かりな作業になるため、なかなか手を出しにくいものです。しかし最適化されたレイアウトには、それを上回る様々なメリットがあります。
コストの削減
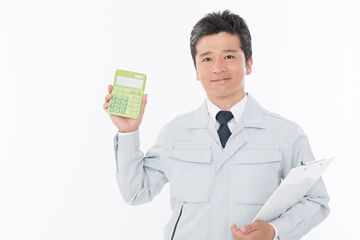
効率的な倉庫レイアウトは最終的にコストの削減になります。
無駄な動きを省いてスムーズに作業が進めば、それだけ人件費の削減になります。デッドスペースを削減して保管スペースを増やすことができれば、倉庫の拡充を避けたり遅らせたりすることができ、それだけコスト削減になります。逆に広すぎるスペースを見直せば、管理費の削減にも繋がります。
今ある倉庫を最大に有効活用することで、余分なコストを削減し、且つ作業効率を向上させるのがベストな状態です。
棚卸しの精度向上
コストに直接影響を与える在庫管理は慎重に行わなければなりませんが、倉庫が雑然としてくると、棚卸しの精度を維持するのに余分な労力を使うことになります。きちんと整理整頓された保管庫、そして在庫の動き方や動線を意識した倉庫レイアウトが最適であれば、在庫管理、棚卸しの精度向上に役立ちます。
ミスや事故の予防
倉庫レイアウトが業務や動線、出入りする人数、在庫数に見合っていないと、誤出荷や遅配などの業務上のミスに加え、倉庫内の思わぬ事故を生む恐れがあります。もしそれらが見合っておらずスムーズに業務が行えない場合は、レイアウトを改善することが急務です。
倉庫レイアウトを改善する際のポイント
倉庫レイアウト改善のメリットをご紹介しましたが、それを踏まえて、どこを重視して見直していけば良いのかを解説します。作業効率の向上に欠かせない3点をピックアップしました。
作業時間の短縮
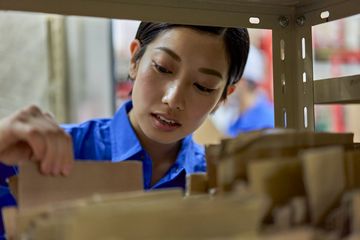
倉庫での作業工程を整理し、入荷から出荷までの間に、無駄な動きをしていないか見直します。動線が重複、錯綜していないか、頻繁に出入りのあるアイテムの保管場所が複雑な場所にないかなどです。
出荷頻度と保管場所が合っているかは、作業効率の向上に欠かせないポイントです。工程ごとに最短の時間で業務ができるように、レイアウトを組んでいきましょう。
安全性の向上
多数の従業員と大量の在庫が出入りする倉庫は、安全性がとにかく重要です。什器の固定は大前提として、重たいアイテムが頭上の棚に並んでいないか、通路に在庫等を直置きしていないか、避難経路を什器や在庫で塞いでいないかなどをチェックします。倉庫のレイアウトを見直すタイミングで、一度倉庫の安全性についても見直すと良いでしょう。
スペースの確保
在庫で倉庫がパンパン、通路も塞ぎ始めている…というタイミングで、新たな倉庫の拡充を考慮することがあります。しかしその前に、レイアウトの見直しや什器の買い替えなど、改善できる余地がまだあります。
特に什器は、倉庫業務を快適にするひとつのカギです。デッドスペースを削減して空間にスペースを生み出せないか、その空間にぴったりはまる棚はないかを調査し、保管スペースを増やしましょう。これもレイアウト改善のポイントです。
倉庫レイアウト改善の流れ
それでは、実際に倉庫の業務フローに合わせてレイアウトを改善する方法を、流れに沿って解説していきます。
1.現状の問題点整理
前章で挙げた改善のポイントを、より具体的に掘り下げていきます。
まずは、現状の倉庫のレイアウトを書き出します。そして1日の業務フローに沿って、動線をレイアウト上に書き込んでみます。
動線や什器の配置に問題がないかチェックし、あれば見直しへ。移動距離が長すぎたり、保管場所が複雑すぎたりしないか(探す時間に無駄がないか)もチェックします。
作業効率を上げるためには、商品をピッキングする従業員に無駄のない動きをしてもらうことが重要です。そのために、物理的な無駄があれば新しいレイアウトで改善していきます。
また、紙上ではわかりにくい問題点として、通路の狭さがあります。人がすれ違えない通路は、待ち時間が発生して効率が良くありません。かと言って広すぎる通路は、スペースロスに繋がります。業務に見合った通路の幅になるよう、こちらも見直しのチェックリストに入れましょう。
2.全体のレイアウト決定
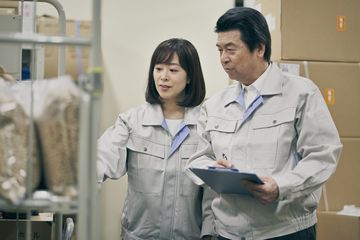
問題点を整理したら、それを元にレイアウトを決めていきます。
次の章でレイアウトの基本について詳しく解説していますが、行き止まりは非効率になるため、可能ならば一筆で回れるような配置が望ましいでしょう。
3.保管場所の決定
レイアウトを決めたら、最後に保管場所を決めます。出荷頻度の高いアイテムは取り出しやすい位置に、低いものは奥に保管します。
この時に重要になる出荷頻度については、「ABC分析」で分類しておくと効率的です。
Aは売り上げの多くを占める、出荷頻度の高い商品。欠品を避け緊張感を持って管理したい部類です。作業効率が優先です。
Bは売れ行きが平均的で現状維持でいける商品。定期的に発注するか、在庫が切れたら発注します。作業効率と保管効率はバランス良く。
Cは出荷頻度が低く、在庫が切れたら発注すれば良い商品です。保管効率が優先です。
このように分類し、手前から順にA→B→Cと保管していきます。
倉庫レイアウトの基本形
ここでは、基本のレイアウトの型を2タイプご紹介します。これを元に、自社倉庫に合わせてレイアウトを組みます。一筆書き、もしくはそれに近い形が理想です。
【基本レイアウト】I型レイアウト
I型レイアウトとは、入荷から出荷までの作業フローを、順に直線に並べていくスタイルです。例えば一列目から入荷→入荷検品→保管(ピッキング)→出荷検品…というように列ごとに配置し、最後に出荷の列を置きます。入り口と出口が両側にある倉庫に適しています。
倉庫に広さが無い場合でもレイアウトを組みやすいのがメリットです。逆に広い場合、入荷側と出荷側でコミュニケーションがとりにくいことがデメリットとなります。
【基本レイアウト】U型レイアウト
U字レイアウトとは、入荷をスタート、出荷をゴールとしてUの字を描くように作業フローを並べるレイアウトです。例えば入荷→入荷検品と進み、倉庫の奥が保管スペースになります。そして出荷検品→出荷のような具合で戻ってきます。入荷と出荷は倉庫の同じ側(入り口付近)になります。
入荷と出荷が隣り合わせのため、コミュニケーションが取りやすく、作業分担や応援がしやすいのがメリットです。しかし、十分なスペースが確保できない倉庫では、各作業のスペースが狭くなります。
倉庫レイアウトのコツと注意点
その他、レイアウトを組む際に知っておくと良い、細かいコツや注意点をまとめました。
出荷頻度の低いものを上へ
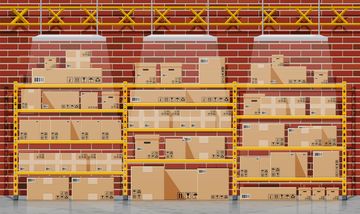
背の高い棚やスチールラックなどを導入した際、出荷頻度の低いものは上に保管します。逆に出荷頻度の高いものは、手に取りやすい高さに保管します。先にご紹介したABC分析で例えるなら、Cが上部、Aがアクセスしやすい高さ、Bが下段となります。
ただし、落下すると危険な重いものや、大きくて角があるものなどは、Cでも下部に置くなど安全性にも配慮しましょう。
保管効率と作業効率はバランスよく
倉庫のレイアウト改善を行う中で、つい収納力、保管効率を優先してしまうことがあります。「商品が倉庫に収まらない」ことは、すぐに作業効率の低下となってあらわれ、業務に差支えがあるからです。
しかしあまりに保管効率ばかりを意識しすぎると、出荷頻度に関わらずに、出し入れしにくい場所に「とりあえず」収納してしまうようなことが起こります。これもまた、後々作業効率向上の妨げとなります。
保管効率と作業効率は、いつでもバランスを保てるように注意が必要です。
作業スペースは広すぎず狭すぎず
倉庫には保管スペースと共に、検品や入出荷作業を行う作業台が必要です。これは、広すぎるとスペースロスに、狭すぎると効率が悪くなるため、作業人数に合わせたものを準備しましょう。送り状発行のためのプリンター等は近くに置きます。
デッドスペース対策にはスチールラックが有効
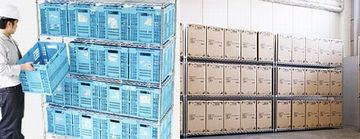
棚や作業台を無駄なくレイアウトした倉庫でも、探すと意外な所にデッドスペースが見つかることがあります。大型の什器が入りきらない隙間などがそうですが、そんな時はスチールラックを活用するのがおすすめです。隙間に合わせて幅を選ぶことができ、少しのスペースに棚を追加できます。また、高さのサイズも豊富なので、天井近くまで保管スペースを作ることも可能です。
おわりに
作業を効率化しながら安全性を保ち、保管効率も上げていくような改善を成功させるには、最初に問題点を全て出し切ることが大切です。日頃から、倉庫の使いにくさなどに目を配り、倉庫で働く従業員の言葉に耳を傾けるようにすると、次の改善に役立てることができます。作業効率の向上、コスト削減のためにも、定期的に倉庫レイアウトの見直しをしていくのがおすすめです。
-
2025.04.01安くて丈夫なスチールラックの選び方!失敗しないポイントを解説「安いスチールラックを買ったけど、すぐに歪んでしまった…」「思ったより耐荷重が弱く、収納したいものが載せられない…」とお悩みの方も多いのではないでしょうか。スチールラックは手頃な価格で購入できる一方で、選び方を間違えると […]
-
2025.02.25納戸の収納術を徹底解説!便利なアイテムやスペースを活用するコツとは?「物であふれかえった納戸を何とかしたい」「狭い納戸でもすっきり収納できるアイテムはないの?」とお悩みの方もいるのではないでしょうか。衣類や寝具、家電などさまざまな物を収納するのに便利な納戸。普段使わない物をしまっておく場 […]
-
2023.07.14洗濯物が増える夏場に向けて 洗濯機・洗面所まわりの収納の選び方こんにちは、ルミナスクラブです。いよいよ、日本全国、暑くなってきましたね。熱中症対策など、していますでしょうか。普段より汗をかくことも多いこの季節。着ている衣類だけでなく、タオルを使うことも増えて洗濯物の量が増えていない […]
-
2023.05.26梅雨こそ、読書を満喫。 快適に過ごせる本棚の選び方こんにちは、ルミナスクラブです。5月になって夏日を記録する日があるなど、暖かいというより暑い日も増えてきましたね。前回、ルミナスクラブでは、夏の前に訪れる「梅雨」をテーマに部屋干し・室内干しに最適な商品をご紹介させていた […]
-
2023.05.12快適に、梅雨を乗り切れ! おすすめの部屋干し・室内干し対策こんにちは、ルミナスクラブです。みなさま、ゴールデンウイークは何をして過ごしましたか?今年は平日もうまく休めたら9連休と、比較的長いお休みを過ごせた人もいたのではないでしょうか。事前の予報では全国的に雨になるような話をあ […]
-
2023.04.28春の新生活準備 第2弾 揃え忘れていた収納ありませんか?キッチン収納編ここんにちは、ルミナスクラブです。4月も始まり、いろいろと新しい環境になり、新生活を始めている方もたくさんいると思います。ルミナスクラブでは今年の2月に『新生活』をテーマにしたコラムを配信させていただきました。 春の新生 […]
- 書類整理
- 一人暮らし
- 子供部屋
- テンションラック
- キッチン家電
- 収納棚
- 部屋
- ディスプレイラック
- 倉庫
- 玄関収納
- アンティーク
- 収納ボックス
- ラック
- 屋外
- キャンプ
- オフィスチェア
- 収納術
- インダストリアル
- カフェ風
- 突っ張りラック
- レンジ
- 庭
- キャンプ用品
- テレワーク
- アイデア
- デスク
- 和風
- お風呂
- システム収納
- おしゃれ女子
- 洗濯機
- 椅子
- 見せる収納
- ディスプレイ
- パソコン
- 掃除
- おしゃれ
- 整理整頓術
- 洗濯機上
- キッチン
- 衣類収納
- DIY
- 浴室
- 商品
- コツ
- フック
- ワンルーム
- ガレージ
- リメイク
- 木製家具
- 店舗
- 方法
- 有孔ボード
- インテリア
- コーディネート
- カラフル
- ハーブ
- レイアウト
- 棚
- 活用法
- スチールラック
- ホワイト
- 本棚
- 1人暮らし
- 効率化
- 漫画
- CD収納
- ナチュラル
- モダン
- ベビー用品
- 洗面台
- 改善
- 中軽量ラック
- 大量
- 転倒防止
- 厨房
- 赤ちゃん
- リビング
- ハンガーラック
- 中量ラック
- おすすめ
- オーディオ
- クローゼット
- オフィス
- キッチンカウンター
- ホテル
- 選び方
- ランキング
- テレビ台
- ペット
- 業務用
- キッチンワゴン
- お家
- 狭い
- 人気
- オフィスレイアウト
- ロースタイル
- ブルックリンスタイル
- ランドリー収納
- キッチン収納
- 収納
- ガーデニング用品
- キッチンラック
- 効率アップ
- レンジ台
- 在庫整理
- イームズ
- 壁面収納
- 書類収納棚
- 収納方法
- 収納家具
- 整理整頓
- ガーデニング
- キャスター
- ミッドセンチュリー
- 対面キッチン
- ベランダ
- 業務用スチールラック
- サイズ